گذر زمان در تار و پود صنعت تولید مفتول: نگاهی به رشد و تحولات تاریخی در قلب صنایع فلزی – بخش دوم
به بخش دوم سفر حیرتانگیز ما در اعماق صنعت مفتول خوش آمدید.
تشکری ویژه برای ادامهٔ همراهیتان – قدمهای بعدی ما بسوی مرزهای تازهای از دانش و نوآوری است. یادآوری میکنیم که این مقاله همچنان فصل دیگری در انتظار دارد که نباید از آن غافل شوید. پس لطفاً برای کسب اطلاعات بیشتر و عمیقتر، بخش پیشرو را از دست ندهید. در انتظار دیدار شما در بخش بعدی هستیم، جایی که اکتشافات ما مستمر خواهد بود.
مواد اولیه مورد استفاده در تولید مفتول
مواد اولیه مورد استفاده در تولید مفتول عمدتاً شامل فلزات و آلیاژهای فلزی هستند که بر اساس خصوصیات فیزیکی و شیمیایی مورد نظر در فرآیند تولید، انتخاب و ترکیب میشوند. این مواد به شرح زیر هستند:
فولاد:
- پایه اصلی برای تولید مفتولهایی با کاربردهای متنوع میباشد. فولادها بر اساس محتوای کربن به انواع کم کربن، متوسط کربن و بالا کربن تقسیم میشوند. فولاد کم کربن (مانند AISI 1010) معمولا برای مفتولهای با خواص انعطافپذیری و خمشی خوب استفاده میشود. فولادهای با کربن بالاتر (مانند AISI 1080) برای مفتولهای با استحکام بالاتر مورد نیاز هستند.
فولاد زنگ نزن (استنلس استیل):
- حاوی کروم، نیکل و گاهاً مولیبدن است که مقاومت در برابر خوردگی و دما را به مفتول میدهد. استفاده از آلیاژهای مختلف میتواند براساس کاربرد مفتول، خواص مکانیکی مطلوبی را فراهم کند.
آلومینیوم:
- استفاده از آلومینیوم و آلیاژهای آلومینیومی به دلیل وزن سبک، رسانایی خوب و مقاومت در برابر خوردگی، عمدتاً در صنایع انتقال برق و ساختمانی مورد استفاده قرار میگیرد.
مس و آلیاژهای مسی:
- مس به دلیل رسانایی عالی الکتریکی و حرارتی برای ساخت مفتولهایی که به عنوان هادیهای الکتریکی استفاده میشوند، مناسب است. همچنین آلیاژهای مس مانند برنج و برنز خواص مکانیکی و شیمیایی متنوعی دارند.
نیکل و آلیاژهای نیکل:
- نیکل و آلیاژهای آن همچون مونل، اینکونل و هستلوی، در محیطهای خورنده و دماهای بسیار بالا استفاده شده و در بخشهایی مانند صنایع شیمیایی، هوافضا و صنایع نفت و گاز مورد استفاده قرار میگیرند.
تیتانیوم:
- یک فلز سبک و در عین حال فوقالعاده استحکام دار که مقاومت خوبی در برابر خوردگی داشته و معمولاً در صنایع پزشکی، هوافضا و در محیطهای شیمیایی استفاده میشود.
مواد پوششدار:
- گاهی اوقات مفتولها را با مواد دیگری مانند روی برای گالوانیزاسیون، پلاستیک یا لاستیک برای عایقبندی الکتریکی پوشش میدهند تا خواص مشخصی مانند مقاومت در برابر خوردگی و رسانایی را بهبود بخشند.
علاوه بر این، برای تولید مفتولهایی با خواص و کاربردهای خاص، ممکن است ترکیبات و عناصر دیگری مثل تیتانیوم، وانادیوم، مولیبدن و صدها عنصر و ترکیب دیگر به فولاد اضافه شوند. این عناصر به دقت انتخاب شده و در نسبتهای مشخص، برای دستیابی به خواص مهندسی مورد نظر مانند مقاومت به سایش، خاصیت انعطافپذیری، استحکام بالا و دیگر خواص مهم، ترکیب میشوند.
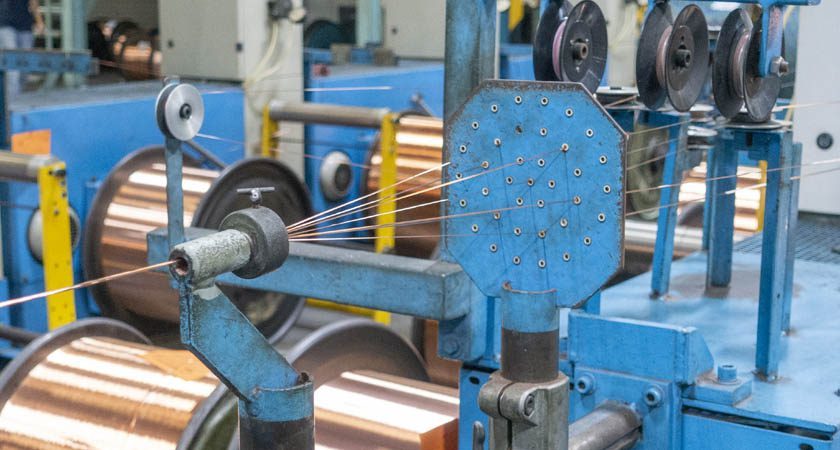
مواد اولیه مورد استفاده در تولید مفتول باید با توجه به خواص مورد نظر مانند سختی، انعطافپذیری، مقاومت در برابر تنش مکانیکی یا شیمیایی، و هدایت الکتریکی یا حرارتی انتخاب شوند. اغلب این مواد با استفاده از فرآیندهایی مانند کشش سرد، نورد، فرآیندهای حرارتی و عملیات سطحی به مفتول نهایی تبدیل میشوند. (مشاهده محصولات مفتول در سایت فروشگاه اطلس پگاه)
3-تاریخچه صنعت مفتول در جهان
صنعت مفتول، که یکی از مهمترین بخشهای تولیدی در زمینهی مصالح و محصولات فلزی است، ریشههای عمیقی در تاریخ دارد. از هزاران سال پیش، انسانها فلزات را استخراج کرده و از آنها مفتولها و طنابهای فلزی تولید میکردند. با پیشرفت تکنولوژی، روشهای ساخت مفتول نیز تکامل یافتهاند.
عصر مفرغ: در این دوره، اولین نمونههای مفتول از مفرغ و برنز ساخته میشدند. از این فلزات به دلیل قابلیت شکلپذیریشان و برای ساخت زیورآلات و اشیاء تزئینی استفاده میشده است.
دوران روم باستان: رومیان از مفتولهای برنزی و مسی برای انواع مصارف از جمله تولید سکه، ساخت زیورآلات و دیگر اشیاء مورد استفاده روزمره بهره میبردند.
قرون وسطی: در این دوره صنعت مفتول شاهد پیشرفتهایی بود. برای مثال، در اروپا مفتول به واسطه استفاده گسترده در زرههای سلسلهای (Chainmail) اهمیت ویژهای یافت.
انقلاب صنعتی: این دورهی تاریخی، که در قرنهای ١٨ و ١٩ رخ داد، نقطه عطفی در توسعه صنعت مفتول بود. توسعه ماشینآلات و امکانات نورد و کشش فلزات امکان ساخت مفتولهایی با قطر کوچکتر و طولهای بلندتر را فراهم آورد و استفاده صنعتی از مفتولها را چشمگیر افزایش داد.
قرن ٢٠ تا به امروز: رشد شدید تکنولوژی و متالورژی، منجر به تولید مفتولهایی با خواص مهندسی پیشرفته شد. صنعت مفتول با پیشرفتهایی نظیر فرآیندهای کشش سرد پیشرفته، فرآیندهای نورد دقیق و کنترل دیجیتالی، که امکان تولید مفتول در طیف گستردهای از ابعاد و با خصوصیات مکانیکی و شیمیایی متفاوت را فراهم آوردهاند، تحولی بزرگ را تجربه کرده است.
امروزه، مفتولهای فلزی در تقریباً هر بخش از صنعت استفاده میشوند، از ساخت سازهها و ماشینآلات گرفته تا تجهیزات الکترونیکی و ارتباطی. برنامهریزی و طراحی مفتولها با استفاده از نرمافزارهای پیشرفته و شبیهسازیهای کامپیوتری انجام میشود تا محصولاتی با دقت فوقالعاده بالا تولید گردند.

نگاهی به اولین روشهای تولید مفتول
اولین روشهای تولید مفتول به دوران باستان برمیگردد که فرآیندهایی بسیار ابتدایی و دستی برای تولید مفتولها استفاده میشد. در این زمانها، فلزات به دست آمده از استخراج معدن و یا بازیافت اشیاء فلزی قدیمی، ابتدا تحت حرارت قرار میگرفتند تا نرم شوند.
- کشش دستی: پس از گرم شدن، فلز را به وسیله چکشکاری به شکلهای پایهای و نیمهآماده درمیآوردند و سپس از طریق کشیدن دستی فلز از طریق قالبهای سوراخدار یا ماتریسها (دایسها)، فلز را به تدریج به فرم مفتول مورد نظر با قطر کمتر درآورده و طول آن را افزایش میدادند.
- نورد دستی: برای فلزات نرمتر مانند طلا و نقره، همچنین ممکن بود از فرآیند نورد استفاده میشد، که در آن فلز بین دو سیلندر دوار که با دست چرخانده میشد عبور داده میشد تا به شکل و ضخامت دلخواه نورد شود.
- چکشکاری: در این روش، فلز گرم به وسیله چکشها به تدریج به قطر مورد نظر رسیده و از این طریق به شکل مفتول درمیآمد.
این روشهای اولیه همچنین اغلب در شرایط سخت کارگاههای کوچک و بدون کنترلهای دقیق انجام میشد و به نیروی انسانی زیادی نیاز داشت. با پیدایش انقلاب صنعتی، تکنولوژیهای جدیدی مانند نورد خودکار و ماشینهای کشش پیوسته روی کار آمد که توانست بهرهوری را افزایش دهد و کیفیت مفتولهای تولیدی را بهبود ببخشد.

تکامل فناوریها و روشهای تولید مفتول در زمانهای مختلف
تکامل فناوریها و روشهای تولید از زمانهای باستان تا کنون به شکل چشمگیری جریان یافته است. روشهای تولید دستی ساده، همانند کشش فلز از ماتریسهای سوراخدار، جای خود را به فرآیندهای مکانیزه دادهاند که امکان تولید انبوه و دقت بسیار بالا را فراهم میآورند.
انقلاب صنعتی: از جمله مهمترین تغییرات در تکنولوژی تولید با آغاز انقلاب صنعتی رخ داد، که دستگاههای نورد مکانیزه و ماشینهای کشش اتوماتیک را وارد صحنه کرد. این تجهیزات، با چرخاندن سیلندرهای دوار و استفاده از انرژی مکانیکی، امکان تولید مفتولهای با قطر یکنواخت و طولهای زیاد را فراهم آوردند.
قرن 20: در قرن بیستم، توسعهی متالورژی و مهندسی مواد، همراه با نوآوریهای بیوقفه در ماشینآلات تولید، به بهبود قابلیتهای تولید مفتول و همچنین خواص مهندسی فلزات کمک کرد. روشهای تولید انواع مفتولهای فلزی پیشرفتهتر شدند و به انعطافپذیری بیشتر در طراحی و تولید انواع محصولات انجامید.
روشهای نوین: عصر دیجیتالی و اتوماسیون صنعتی بستری را فراهم آورد که در آن ماشینآلات با دقت بسیار بالا و کنترلهای کامپیوتری، نقش اساسی در تولید دارند. روشهای تولید مداوم، نورد سرد و گرم، کشش، و فرآیندهای پیچیدهتر مانند عملیات حرارتی پیشرفته و عملیات پایانی مانند پوششدهی و تمام کردن سطح، باعث تولید مفتولهایی با مشخصات مختص به کاربرد خاصی شدهاند.
رویکردهای پایدار: به تازگی، رویکردهای تولید پایدار و مسئولانه محیط زیستی نیز به این صنعت راه پیدا کردهاند. با استفاده از روشهای بازیافت فلزات و فرآیندهای کمتر آلاینده، صنعت مفتول نه تنها به کارایی و بهرهوری بیشتر دست یافته بلکه کوششهایی نیز در جهت حفظ محیط زیست از طریق کاهش انتشار گازهای گلخانهای و مصرف بهینه منابع انجام میدهد.
بنابراین، از کشش دستی سنتی تا استفاده از تکنولوژیهای پیشرفتهی امروزی، روشهای تولید مفتول نمونهای از پیشرفت چشمگیر در تکنولوژی و بهبود مستمر در فرآیندهای تولیدی هستند.

4-نوآوریها و پیشرفتهای کلیدی در صنعت مفتول
صنعت مفتول توانسته است با پذیرش نوآوریهای پیوسته و پیشرفتهای فناورانه گامهای بزرگی را به سمت توسعه و کارایی بیشتر بردارد. میتوان چندین نقطه کلیدی از این پیشرفتها را برشمرد:
- اتوماسیون و کنترل دقیق فرایند: مکانیزاسیون و کنترلهای دقیق کامپیوتری امکان تولید مفتولهای با دقت بسیار بالا و قابلیت تکرارپذیری را فراهم کردهاند. این امر همچنین افزایش چشمگیری در بهرهوری و کاهش هزینههای تولید را به دنبال داشته است.
- تکنولوژیهای نورد پیشرفته: نورد چندمرحلهای، نورد پایانی ممتد و نورد سرد از فناوریهایی هستند که به تولید محصولات با کیفیتی بالاتر و با قطرهای دقیق کمک کردهاند.
- عملیات حرارتی مدرن: پیشرفتها در عملیات حرارتی مثل عملیات آنیلینگ به کنترل بهتر خواص مکانیکی مفتولها کمک کرده و انعطافپذیری آنها را افزایش داده است.
- روکشهای جدید و پوششهای سطحی: استفاده از پوششهای محافظتی مانند گالوانیزه کردن، روکش پلاستیکی یا لاستیکی، دارای مزایای تعیینکنندهای از قبیل افزایش طول عمر و بهبود خواص آنتیباکتریال و مقاومت در برابر خوردگی هستند.
- فناوریهای بازیافت و دوباره پذیری: پیشرفتهایی در بازیافت مفتول و مواد اولیه از ضایعات، به کاهش هزینهها و اثرات زیستمحیطی صنعت کمک کرده است.
- مهندسی مواد: توسعه آلیاژهای جدید و بهبود خواص مواد مانند استحکام بالا، مقاومت در برابر خوردگی و وزن سبک، نه تنها به ارتقای کیفیت عمومی مفتولها کمک کرده بلکه امکان استفاده از آنها در کاربردهای نوین مانند صنایع هوایی و خودروسازی را ممکن ساخته است.
نوآوریها و پیشرفتهای موجود در صنعت تولید مفتول به همراه پیشرفتهای آتی، بطور مداوم در حال توسعهی کاربردها و بهبود کیفیت محصولات هستند. این صنعت همچنان یکی از متحرکترین و تأثیرگذارترین بخشهای تولیدی باقی خواهد ماند.